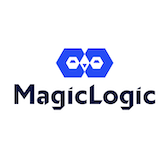
The Future of Automated Warehouses: Trends and Technologies You Need To Know
by MagicLogic
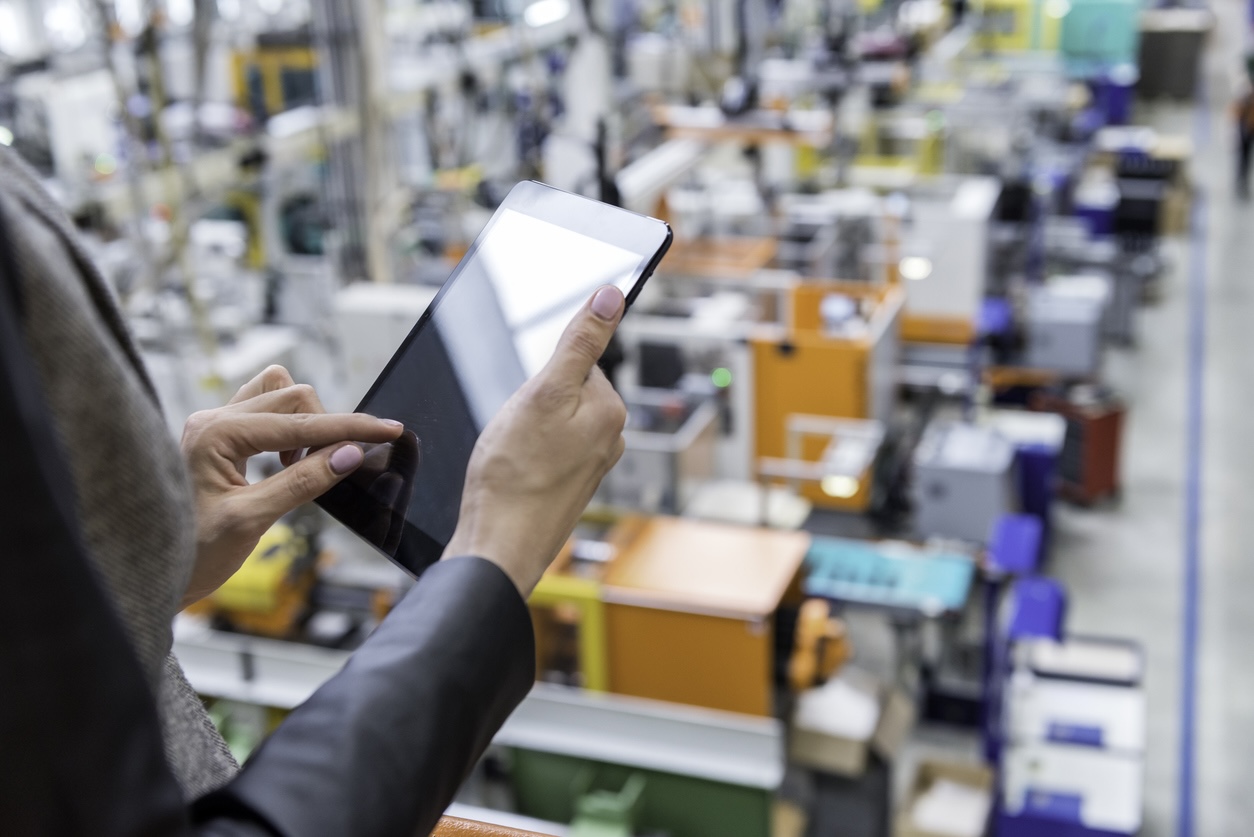
While warehouses all have the same goal—efficiently storing inventory until it’s time to ship it to customers or store locations—they achieve that goal in very different ways. Some are ultra-modern, with high-tech robotics and few human workers. Others still rely largely on manual labor for picking, packing, data entry, and more.
But one thing is certain: to stay competitive in a world where supply chain disruptions are the new normal, warehouses that depend on manual processes need to adapt.
Logistics leaders recognize this fact, and many of them are already taking steps to future-proof their fulfillment operations. What will 2025 bring for their businesses? In this article, we discuss four trends (and the associated technologies) that will shape this year’s warehouse innovations.
This article is the third in a series focused on warehouse automation and load planning technology. Read the others here:
- The Rise of Robotics in Warehouses: How Automation Is Changing the Game
- How Automation and Load Planning Work Together To Optimize Warehouse Efficiency
- Overcoming the Challenges of Warehouse Automation: What You Need To Know Before Making the Leap
Trend #1: Automation efforts will start with software
Warehouse automation isn’t just about robotics whizzing around the floor—it starts with having the right software to orchestrate every move.
“Software [is] your foundation. A software system that is connected to your inventory and your equipment can help you have increased inventory accuracy, which then contributes to increased order accuracy, which then contributes to fewer returns.” — Kim Baudry, Warehouse Automation and Sustainability
With a variety of software solutions at their fingertips, business leaders looking to automate their warehouses in 2025 will start with the fundamentals of fulfillment: inventory management, picking, packing, and shipping.
- Warehouse management system (WMS). A WMS is the backbone of an automated warehouse, providing real-time visibility into inventory and coordinating tasks like picking, packing, and replenishment.
- Enterprise resource planning (ERP) system. An ERP connects warehouse operations with other business departments, allowing data to flow smoothly and leading to better forecasting, resource allocation, and decision-making. One survey found that 38% of warehouses planned to deploy a WMS or ERP in the next 12 months.
- Load planning software. Load planning software optimizes how goods are packed into trucks or containers, maximizing space and reducing shipping costs. Whether you use packing automation tools or manual processes, load planning software helps ensure that products are handled as efficiently as possible.
- Shipping software. Shipping software automates carrier selection, label generation, and tracking updates, speeding up order fulfillment and providing customers with faster, more accurate delivery information. As automation expert Kevin Gaul puts it, “I strongly believe that the biggest bang for your buck is going to be with automating your shipping process. … Your shipping costs are going to eat almost all of your other costs bar none.”
Trend #2: Robotics will continue to rise in popularity
With businesses looking for ways to boost efficiency and handle growing order volumes, warehouse robotics are becoming more widely adopted. As this technology becomes more accessible and integration with software improves, even small and mid-sized warehouses will reap the benefits of robotics-driven automation.
A 2025 report has found that the areas that logistics leaders are most interested in improving in their warehouses and distribution centers are capacity utilization (67%), order accuracy (58%), and packaging (49%).
The technologies they’re planning to upgrade or implement to achieve their goals include the following:
- Mobile collaborative robotics
- A-frame picking technologies
- Picking robotics
- Palletizing robotics
- Automated packaging solutions
- Automatic guided vehicles
Let’s take a closer look at just two types of robotics that are growing ever more popular.
Collaborative robots (cobots)
Collaborative robots, or cobots, are designed to safely work alongside human workers in shared spaces. They’re equipped with advanced sensors and safety features to avoid collisions and adapt to their environments in real time.
Collaborative robots can take various forms. For example, a cobot might consist of various robotic arms that help with repetitive tasks like picking, packing, or sorting items on conveyor belts.
For larger loads, palletizing cobots help stack boxes onto pallets with precision and speed—and they work even better when paired with palletization software that determines optimal stacking configurations.
Autonomous mobile robots (AMRs) and automatic guided vehicles (AGVs)
Both autonomous mobile robots (AMRs) and automatic guided vehicles (AGVs) can be used to quickly transport materials through a facility, but they work a little differently.
AMRs are smart, self-navigating robots that use sensors, cameras, and mapping software to move around a warehouse. AGVs, on the other hand, follow fixed routes, usually guided by magnetic strips, wires, or pre-programmed markers on the warehouse floor.
According to a Gartner report, “Smart mobile robot adoption in supply chains is growing rapidly and will far outpace drones over the next three years. … It’s likely companies will have hundreds, if not thousands, of mobile robots in use.”
Getting started …
If you’re looking to implement a new software system in your warehouse—or go fully robotic—it's useful to consult with experts like Summit Advisory Team. With years of deep supply chain experience, these professionals can help you get new systems integrated with minimal disruption to your current operations.
Trend #3: Artificial intelligence (AI) and machine learning (ML) will take center stage
In the past few years, artificial intelligence (AI) and machine learning (ML) have become differentiators in the supply chain world. By enabling smart, dynamic decision-making, these technologies pave the way for physical automation solutions that can cut down on manual labor.
Data analysis and beyond …
What exactly can AI and ML technology do in your warehouse? Consider these use cases:
- Data analysis and decision-making. AI can analyze operational data to identify patterns and predict future demand, helping shippers make smarter decisions that improve efficiency and reduce costs. (Check out EasyPost’s new shipping AI, Luma, to learn more about the power of AI for shipping optimization.)
- Tracking and monitoring. Machine learning algorithms are useful for monitoring the movement of goods and equipment, analyzing IoT data to make sure inventory is safely stored or set to arrive on time.
- Picking. AI-powered robots can handle multiple tasks instead of just one, adapting to shifting situations and settings. This makes them ideal for tasks that require precision and accuracy, including picking, packing, and sorting.
- Inventory management. Machine learning models are often used to forecast stock levels based on historical trends and demand patterns, helping to prevent stockouts or overstocking.
How to incorporate AI into your warehouse operations
Expert guests on the Unboxing Logistics podcast agree: While it’s exciting that AI has countless possible uses, the best course of action is to start small, choosing tools that solve specific challenges in your operations.
Henrik Bergsager from Powerhouse AI says, “AI tools are more agile now, so you can target the operation that is important for you to automate. [For example,] you can focus AI on tools related to inventory management, or demand forecasting, or … optimizing your storage. By focusing on these smaller cogs in the warehouse, you don't need massive amounts of investments to get up and running.”
Similarly, Chris Caplice, director at the MIT Center for Transportation Logistics, notes that “the [projects] that seem to be the most successful are the ones that are identifying a problem and saying, “Hey, gen AI might work here,” rather than, “I've got a gen AI hammer, let me find something [to hit].”
Trend #4: Sustainability concerns will drive automation adoption
The cost-cutting benefits of automation are undeniable, but another concern is also motivating business leaders to phase out manual processes: sustainability.
The consumer perspective
You’ve probably heard that sustainable brands have a competitive edge. But is this true? Do consumers really care about the eco-friendliness of the merchants they buy from? The answer, for many, is a resounding yes. A PwC study reveals that 46% of people are buying more sustainable products in an effort to reduce their environmental impact, and 80% are willing to pay more for sustainable goods.
Automation and sustainability go hand in hand
Warehouse automation can drive greener operations in several ways. As one example, implementing automated storage systems, which make efficient use of vertical space, allows organizations to reduce warehouse footprints. A smaller building means lower consumption of energy for lighting, heating, and cooling—and lower carbon emissions.
Why packaging and load planning matter
Packaging also plays a major role in sustainability efforts. More and more merchants are turning to automation technology to not only pack boxes and load pallets, but also to optimize box sizes, pallet configurations, and truckloads. These technologies minimize wasted space and reduce packaging materials, two outcomes that are great for both your wallet and the planet.
Kim Baudry recommends “using packaging equipment that doesn't require a lot of air and builds a package around an individual item or a group of items,” adding that “with software and automation … [you can] build out the cube of your outbound truck better, so we have fewer trucks on the road.”
Future-proof your fulfillment with MagicLogic
Warehouses are changing—and the pace of progress won’t slow down anytime soon. To keep up with customer demand (and outpace the competition), companies of all sizes need to automate their operations with the right equipment and software.
When it comes to packing and load planning, MagicLogic is the ideal solution for optimizing decision-making, minimizing wasted materials, saving on shipping costs, and reducing carbon emissions.
Able to integrate seamlessly with your warehouse software, MagicLogic helps with cartonization, palletization, and truckload configurations.
Learn how MagicLogic can help future-proof your fulfillment.