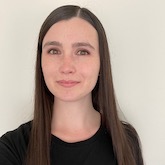
What Is a Logistics Center? Its Role in the Supply Chain
by Jaidyn Farar
As your business grows, shipping products to customers gets complex. With more orders flowing in each day, your fulfillment operations need to scale fast to keep up.
Logistics centers are the heart of your order fulfillment operations. The essential activities you perform at these facilities determine whether customers receive packages on time and intact.
What are logistics centers, and what’s their role in the supply chain? This article delves into these questions, providing a clear understanding of logistics centers and their indispensable role. It also explores the various types of logistics centers—distribution centers, fulfillment centers, on-demand warehousing, cross-docking facilities, and dark stores—each with its unique characteristics.
By understanding these different types, you can better determine which one aligns with your business's needs, optimizing your logistics strategy for superior performance and customer satisfaction.
What are logistics centers?
Logistics centers are facilities dedicated to logistics activities. These centers include space, equipment, and technology for receiving, storing, packaging, and distributing goods.
Often located near major transportation hubs, logistics centers are key elements of the supply chain, facilitating the smooth flow of goods from manufacturer to customer. Efficient logistics centers improve the speed, accuracy, and cost of delivery.
Note: Unlike warehouses, which are used only for storage, logistics centers are also used for order fulfillment.
What do logistics centers do?
Logistics centers help control the flow of goods through the supply chain, streamline inventory distribution, and allow for cost-effective order fulfillment.
Every logistics center works a little differently. This section will provide an overview of some of their most common functions, and later we’ll delve into the differences between the five types of logistics facility.
Receive inbound shipments
Logistics centers constantly receive inbound shipments, which are unloaded, sorted, and assigned to a storage location. The receiving process involves verifying shipment information—including packing lists, bills of lading, and delivery receipts—and inspecting products for damage or quality issues.
Store and manage inventory
Most logistics centers include shelves, bins, and racks where inventory is stored. Staff members take care of inventory management tasks such as the following:
- Allocating storage space for incoming stock based on characteristics like size, weight, and special storage requirements
- Labeling inventory with identification tags, barcodes, or RFID tags for accurate tracking and retrieval
- Conducting regular inventory counts and audits to maintain accurate records
- Monitoring inventory levels and reorder points to ensure optimal stock levels and prevent stockouts or overstocks
Process orders
Order fulfillment is one of the most crucial functions of a logistics center. This process can be streamlined using technology and usually involves the following steps:
- Receive and process customer orders
- Pick items from inventory using picking lists, order tickets, or automated picking systems
- Pack products securely using appropriate packaging materials and methods
- Generate shipping labels and documentation for outbound shipments
- Coordinate with shipping carriers to schedule pickups and arrange delivery
- Notify customers of shipment status and tracking details
Process returns
Finally, just as logistics centers handle outbound shipments to customers, many also receive shipments from customers—products that customers return due to damage, the wrong fit, or other reasons. Once these returned items arrive at the logistics center, they’re inspected and either reincorporated into inventory, refurbished, recycled, or discarded.
What can you find in a logistics center?
While every logistics center will look different, they generally include many of the same elements. Certain storage solutions, equipment, and technology ensure that every necessary logistics activity can take place. So, what can you expect to find in a logistics center?
- Warehousing: Large storage areas for holding goods
- Loading docks: Platforms or bays equipped with ramps, doors, and loading equipment (such as forklifts, pallet jacks, and conveyors) for loading and unloading trucks
- Order processing areas: Dedicated zones for receiving, picking, packing, and preparing orders for shipment
- Shipping and receiving areas: Designated zones for receiving incoming shipments, inspecting goods, documenting arrivals, and processing outbound shipments
- Material handling equipment: Various types of equipment and machinery used for moving, handling, and transporting goods, such as forklifts, pallet jacks, reach trucks, and conveyor systems
- Technology infrastructure: IT systems, software, and communication networks to support inventory management, order processing, tracking, and other logistics operations
Different types of logistics centers
What are the different types of logistics centers? While most logistics centers have a lot in common, they also have key differences in their setups and functions. To know what type of logistics center to use for your own business, you’ll need to understand what each type does.
Distribution centers
Distribution centers (DCs) are transit hubs where finished goods are received, stored, processed, and shipped. Though they’re often used to fulfill customer orders, products can also pass through distribution centers on their way to another DC or to restock brick-and-mortar stores.
Businesses that operate their own distribution centers choose their locations strategically to ensure that inventory is easily accessible to customers. By placing distribution centers near the majority of your customers, you’ll speed up the delivery process and save money on shipping.
Fulfillment centers
Fulfillment centers are distribution centers owned and operated by third-party logistics providers, or 3PLs. Businesses ship their inventory directly to the 3PL’s fulfillment center, where it’s stored. When customers place orders, 3PL workers pick, pack, and ship the products.
A 2024 report provides insight into the value-added services that fulfillment centers provide: “Today’s 3PLs go beyond moving products from point A to point B. They provide services related to data management, analytics, inventory visibility, and network optimization.”
If you use a fulfillment center, you won’t need to worry about renting warehouse space, buying equipment or technology, or hiring staff to fulfill orders. On the other hand, you’ll have less oversight into your day-to-day order fulfillment processes.
On-demand warehousing
On-demand warehousing is a service that finds available warehouse space for businesses to temporarily store inventory and fulfill orders. The on-demand warehousing provider acts as a middleman; it’s a bit like Uber, but instead of matching drivers to passengers, on-demand warehousing matches businesses to warehouse space.
Unlike 3PLs, on-demand warehousing doesn’t require a long-term commitment (or minimum order volumes), making it a more flexible solution. Using these temporary storage and fulfillment solutions can be a good way to expand your logistics network and test new markets, especially in situations when demand fluctuates a lot.
That may be why one on-demand warehousing provider saw its enterprise users grow 128% year over year in 2020, when the Covid-19 pandemic hit and ecommerce orders surged.
Cross-docking facility
A cross-docking facility is similar to a distribution center, but it lacks one key element: storage space. Goods are received, sorted and consolidated, and quickly loaded into outbound vehicles to be transported to their next destination. The cross-docking facility is simply a stopping point between a shipment’s starting and ending points.
These types of facilities are often used when transferring goods from one DC to another or to restock physical stores.
Dark stores
Dark stores are retail locations that have been converted into distribution centers. Most dark stores aren’t open to the public, but local customers can take advantage of curbside pickup and home delivery services. Some dark stores leave part of a store open for in-person shoppers and convert the rest of the floor plan into a distribution center.
Large retailers like Walmart and Best Buy have experimented with this model.
Warehouse automation analyst Rueben Scriven writes that while he expects the number of dark stores to rise drastically by 2030, “The pathway to success won’t be straightforward—after all, this is an asset-heavy business model which can be difficult to undertake profitably.”
The role logistics centers play in ecommerce
Logistics centers play a vital role in ecommerce. Without facilities dedicated to storing, picking, packaging, and shipping inventory, it would be virtually impossible to keep up with high order volumes, especially during peak season.
If you’re running your own distribution center, it’s essential to optimize your processes, train your staff, and implement the latest technology to keep things running smoothly.
EasyPost provides a variety of resources to help you run your facility as efficiently as possible. Get started with the following articles and podcast episodes:
- Article: What Is Third-Party Logistics (3PL), and Do I Need It?
- Article: How to Ship Products to Customers: A Step-by-Step Guide
- Article: How To Build a Great Pick and Pack Process for Your Business
- Podcast: Choosing the Right 3PL With Adam McCoy From eHub
- Podcast: Warehouse Automation and Sustainability With Kim Baudry From Dematic
If you’re looking for a solution to simplify shipping, we can help with that too! EasyPost’s suite of shipping APIs makes it simple to integrate with carriers, generate shipping labels, and save money on order fulfillment.