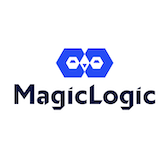
The Rise of Robotics in Warehouses: How Automation Is Changing the Game
by MagicLogic
By the end of 2027, over 25% of warehouses are expected to be automated—up from 18% at the end of 2021. Why are more organizations making the move toward automated facilities? And is automation worth the investment?
This article will examine some of the most pressing challenges shippers are facing, explain how robotics helps take the pressure off, and reveal the benefits of warehouse automation.
This article is the first in a series focused on warehouse automation and load planning technology. Read the others here:
- How Automation and Load Planning Work Together To Optimize Warehouse Efficiency
- The Future of Automated Warehouses: Trends and Technologies You Need To Know
The pressure to evolve
From high consumer expectations to labor shortages and rising costs, your business faces a host of challenges that demand innovative (and affordable) solutions. Feeling the pressure? You’re not alone. Let’s discuss three major challenges that are hitting businesses particularly hard as we move into 2025.
Rising consumer expectations
Ecommerce has grown rapidly in recent years—spurred largely by the COVID-19 pandemic of 2020—and many organizations have seen incredible success with their online and omnichannel operations. But while the rising popularity of ecommerce means more revenue, it also brings new problems to solve.
Customers have grown used to the two-day delivery and no-questions-asked returns policies offered by ecommerce giants like Amazon. As a result, they now expect lightning-fast delivery, free or cheap shipping, and seamless returns whenever they make an online purchase. In 2024, the average consumer expected packages to arrive in 3.5 days or fewer, and 92% reported that free shipping offers impacted their purchase decisions.
If you fall short of these expectations, you risk losing customer loyalty in an ultra-competitive market.
Ongoing labor shortages
The warehousing industry has been grappling with a shrinking labor pool for years, as older workers have retired and younger ones have set their sights on other industries. These labor shortages translate to increased costs, slower operations, and the inability to scale during peak seasons.
Higher costs
Inflation and supply chain disruptions have driven up costs across the board, from raw materials to transportation. Meanwhile, the cost of renting warehouse space has continued to rise, reaching $9.70 per square foot in 2023. For many companies, these rising expenses threaten already slim profit margins, making it harder to remain competitive.
Every inefficiency in the warehouse—whether wasted space, unnecessary handling, overuse of packaging materials, or suboptimal load planning—can quickly add up, cutting into profits and delaying your growth.
The rise of robotics in the warehouse
Faced with the threat of labor shortages and rising fulfillment costs (plus the constant need to keep customers satisfied), warehouses must evolve—or risk being left behind.
Major businesses have already gotten the memo, building automated fulfillment centers or upgrading existing facilities with cutting-edge automation technologies. For example, Walmart’s latest fulfillment centers feature “automated, high-density storage system[s]” that drastically minimize pickers’ walking distances. Similarly, Duluth Trading Company has recently opened what it calls its “first highly automated fulfillment center” in hopes of increasing order accuracy and speed.
Thinking of adding automation to your warehouses? The following types of robotics help streamline storage, picking, packing, and shipping.
Autonomous mobile robots (AMRs) and automated guided vehicles (AGVs)
Autonomous mobile robots (AMRs) are self-navigating robots that transport goods within a warehouse. They use sensors, cameras, and machine learning to move around obstacles, adapting to an ever-changing warehouse environment in real time. For businesses facing labor shortages, these vehicles decrease the reliance on human workers for repetitive tasks, allowing staff to focus on higher-value activities.
Automated guided vehicles (AGVs) are similar to AMRs, but they don’t adapt to their surroundings in real time. Instead, they use predefined guidelines like marks on the floor, wires, or magnets to travel predetermined paths.
AMRs and AGVs are quickly growing in popularity. One survey found that between 2022 and 2023, the use of these technologies rose from 7% to 20%, indicating that businesses are becoming more comfortable integrating these robots into their facilities.
Automated storage and retrieval systems (ASRS)
Automated storage and retrieval systems (ASRS) use racks, cranes, or shuttles, along with advanced computer systems, to quickly store, locate, and retrieve items. These systems are perfect for handling high-density storage, maximizing both vertical and horizontal space.
Picking products for customer orders is one of the most labor-intensive tasks in a warehouse. By speeding up retrieval times and reducing errors, an ASRS can help you meet the demands of fast-paced order fulfillment and satisfy high consumer expectations.
Automated storage and retrieval systems work closely with warehouse management systems (WMS) and order management systems (OMS) to track where every SKU is stored and locate the right items to fulfill every order.
Goods-to-person (GTP) robots
Goods-to-person (GTP) systems, such as conveyor belts or stacker cranes, bring items directly to picking or packing stations, eliminating the need for workers to traverse the warehouse. Using sensors and mapping technologies, these robots efficiently retrieve bins, totes, or trays containing the necessary products.
By reducing the physical demands on workers, GTP robots make warehouses safer and speed up picking processes. They also reduce costs by minimizing downtime and boosting productivity. Paired with picking software, GTP systems ensure that items are delivered in the optimal sequence for fulfillment workflows.
Sorting robots
Sorting robots identify, group, and route items to the correct destinations within a warehouse. They often use computer vision to recognize items and sort them into bins or onto specific conveyor paths.
Sorting robots are often used for high-volume operations, where speed and accuracy are critical. Their precision minimizes picking and packing mistakes, reducing the costs associated with returns and reprocessing.
Packing robots
Packing robots automate the process of placing items into cartons and securing packages for shipment. With advanced sensors and algorithms, they can handle items of varying shapes and sizes without causing any damage.
These robots work best when paired with load planning technology, which automatically chooses the correct carton size for each order and optimizes product placement to reduce the amount of wasted space in packages. Together, packing robots and load planning software reduce costs by minimizing waste and keeping shipments compact.
Stacking and destacking robots
Stacking and destacking robots specialize in stacking items onto shelves, pallets, or conveyor systems and destacking them for processing. Using sensors, they create stable, space-efficient stacks or break them down as needed.
In addition to saving time, these robots reduce the risk of injuries from heavy lifting and repetitive motions. Their ability to create precise stacks also leads to more efficient use of storage space, lowering the costs associated with wasted space or damaged goods.
Like packing robots, stacking and destacking robots should integrate seamlessly with a load planning system that provides instructions for stable stacking and efficient use of space.
Why invest in warehouse automation technology?
Warehouse automation technology isn’t cheap—and many businesses balk at the cost of implementing new systems. But the long-term benefits make automation worth the investment.
- Higher efficiency. Automation reduces the time spent on manual tasks, with technology handling repetitive processes faster and more consistently than human workers. This improved efficiency means more orders can be processed in less time.
- Lower labor costs. By automating tasks like picking, packing, and sorting, businesses can reduce their reliance on human labor, cutting down on staffing costs, overtime, and training. And with tedious tasks being taken care of by robots, employees have more time to focus on activities that drive business growth.
- More accurate fulfillment. Robots and automated systems reduce the risk of human error in picking, sorting, and packing, leading to more accurate orders and fewer returns. This builds customer trust and allows you to meet high consumer expectations.
- Faster deliveries. Automation speeds up critical processes in the warehouse, from inventory management to order fulfillment. Even during peak periods, automated warehouses can fulfill orders promptly and ensure that packages arrive within the estimated delivery window.
Automate your warehouse with robotics + MagicLogic
Behind every great robot is a powerful software system. And when it comes to packing boxes, palletizing goods, or loading trucks, MagicLogic is the advanced load planning software that every high-volume shipper needs.
MagicLogic enables businesses to automate the packing process from start to finish, taking full advantage of their physical automation technology. It boosts packing efficiency with automatic cartonization recommendations, calculates stable configurations to reduce the chances of product damage, and plans compliant truckloads.