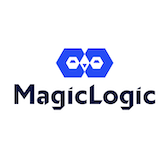
How Automation and Load Planning Work Together To Optimize Warehouse Efficiency
by MagicLogic
When it comes to your warehouses and distribution centers, efficiency is the name of the game.
Seemingly insignificant factors—like where products are stored, the routes pickers take through the building, and packaging decisions—can drastically affect the cost of order fulfillment.
While it’s important to consider the efficiency of every warehouse process, this article will zoom in on some of the most important stages of fulfillment: packing and loading.
When done right, packing boxes and loading up shipments doesn’t have to be labor-intensive, time-consuming, or error-prone. By using a combination of automation technology and load planning software, your business can design an efficient packing process and ensure that every shipment gets out the door on time.
This article is the second in a series focused on warehouse automation and load planning technology. Read the others here:
- The Rise of Robotics in Warehouses: How Automation Is Changing the Game
- The Future of Automated Warehouses: Trends and Technologies You Need To Know
- Overcoming the Challenges of Warehouse Automation: What You Need To Know Before Making the Leap
The need for better load planning
Packing and loading practices vary dramatically from business to business. Some have things down to a science, using technology to select the right box for every package and playing Tetris with freight loads to find the optimal arrangement of pallets. Others rely on individual workers to make decisions about packaging materials and truck loading.
To make your fulfillment process as efficient as possible, you’ll want to fall in the first group, and that requires optimizing your load planning. But what exactly is load planning?
Simply put, load planning is the process of optimizing your packaging, palletization, and truckloads to cut down on wasted space and materials. It involves choosing the right container sizes based on product dimensions and weight, loading pallets correctly to minimize damage and keep products secure, and considering weight distribution and load stability in trucks.
Benefits of optimized load planning
The benefits of optimized load planning include the following:
- More streamlined operations. Planning loads manually is time-consuming and inefficient. An optimized load planning strategy uses automation to reduce manual labor, boost efficiency, and cut down on errors.
- Cost savings. Optimizing your loads reduces shipping costs by avoiding unnecessary trips (saving on fuel and labor), minimizing packaging materials, and reducing carrier fees.
- Time savings. An efficient load planning system involves providing clear guidelines for container usage and placement, helping your team pack and load faster and more systematically.
- More sustainable shipping. By reducing wasted space, materials, and the number of shipments, load planning helps lower your carbon footprint.
- Improved load stability. Proper weight distribution and secure packing ensure that shipments are stable during transit, reducing the risk of damaged goods.
- Compliance. Load planning helps you meet carrier-specific requirements, such as weight limits, axle load distribution, or hazardous material regulations.
Improving warehouse efficiency with automation technology and load planning software
Automation solutions and load planning software go hand-in-hand to improve efficiency.
If robotics are the brawn of warehouse packing and loading operations, load planning software is the brain. It uses order data to make smarter decisions about carton sizes, packaging materials, and truckload configurations—then, robots put the plan into action.
Automation technology
When paired with the right software, machines can handle repetitive tasks like weighing, sorting, and stacking much more quickly and accurately than humans. This allows your team to focus on higher-value tasks.
Technology that’s particularly useful for packing and loading includes the following:
- Automated packaging systems. Automated packaging systems handle tasks like box selection, filling, sealing, and labeling. These machines save time by performing multiple steps in a single workflow. They work best when paired with load planning software, which provides the necessary data on size, weight, and configuration so packaging systems can optimize packing decisions in real time.
- Dimensioning and weighing systems. These systems use sensors and scanners to automatically measure product dimensions and weight. They integrate with load planning software to determine the most cost-effective packaging based on shipment requirements.
- Conveyor and sortation systems. Conveyor systems transport goods through the packing and loading areas, while sortation systems use scanners and automated arms or belts to direct items to their proper destinations. These systems reduce bottlenecks by moving packages quickly and efficiently, helping you scale operations during peak times.
Load planning software
Load planning software like MagicLogic integrates with physical automation solutions, as well as other software systems, to streamline the fulfillment process. But it’s not just useful for businesses using robotics—those with manual packing processes can also benefit from load planning software’s optimized decision-making.
The capabilities of load planning software include:
- Cartonization. Load planning software uses sophisticated rules to automatically select the most efficient container for each shipment, meaning you don’t have to pay to ship air.
- Mixed palletization. If you need to pack multiple different items onto a single pallet, load planning software recommends the best method, taking into account dimensions, weight, stability, and more.
- Freight cubing. Load planning software can calculate the best arrangement of goods within a shipping container. Using space more effectively allows you to reduce the number of shipments required, saving money and cutting down on carbon emissions.
- Truck loading. When shipping freight, load planning software helps calculate axle weights for safe and legal loads, facilitates loading in specific sequences, and handles split-level trucks or trailers.
How True Manufacturing combined automation and load planning software
True Manufacturing, a company that sells commercial refrigerators and freezers, needed a smoother order fulfillment process. Their existing process depended on employee decision-making; when an order came in, a worker would choose the carton size and decide how to physically pack each component.
To reduce shipping costs and packing time, True Manufacturing decided to implement an automated packaging system, which could scan items to determine their length, width, and height.
But they needed something more—a software solution that could receive data from the automated packaging system and guide packing decisions. MagicLogic proved to be the answer.
Communicating with True Manufacturing’s packaging system and ERP system, MagicLogic automatically suggests the optimal carton size and fill material for each order. The carton is then created using the automated packaging system.
During the first year of implementation, the new system reduced packaging expenses by $213,000.
Optimize your warehouse efficiency today
In the market for load planning software? Get in touch with the MagicLogic team to take the system for a test drive and see how it stacks up (pun intended) against your current load planning process.