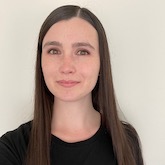
How Warehouse Automation Works (and Getting Started)
by Jaidyn Farar
Warehouses and distribution centers are critical components of the ecommerce supply chain, but these facilities are costly to operate. And many businesses struggle with another challenge: finding and retaining warehouse workers, especially for labor-intensive jobs.
Warehouse automation provides the perfect solution to both of these problems. By automating tedious, error-prone tasks, organizations not only save money but can also provide human workers with more interesting (and less physically demanding) roles, which improves hiring and retention rates.
Given the benefits of warehouse automation, it’s no surprise that automation is on the rise. Gartner analysts estimate that by 2027, over 75% of organizations will have integrated cyber-physical automation into their warehouse operations.
Is warehouse automation the key to lower your costs and improve your fulfillment processes? Keep reading to learn about some of the most cutting-edge automation solutions—and how to choose the right ones for your business.
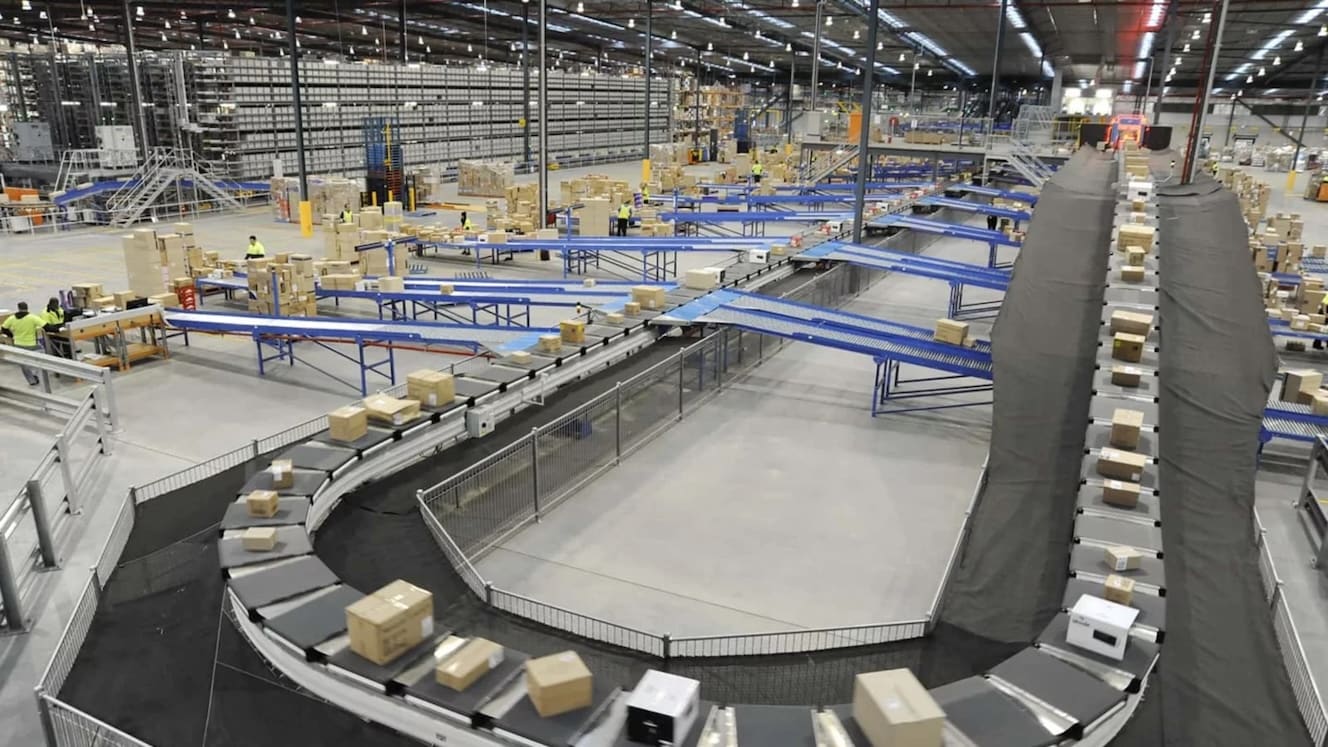
Image courtesy of Dematic
What is warehouse automation?
Warehouse automation is the process of using technology, including software and robotics, to handle tasks like receiving, putaway, picking, packing, and shipping. Automation keeps workers safe and saves time by reducing physical labor, and it reduces errors by eliminating manual data entry.
While the term automation can refer to robotics, robots aren’t the only type of warehouse automation out there. Using software such as a WMS to track and optimize warehouse processes is also a form of automation.
Will automation replace human jobs?
Logistics centers are hives of activity, with many of the same tasks repeated hundreds of times a day. Automation reduces the need for human workers to do these time-consuming, repetitive tasks, leaving them free to do more complex and valuable work. Thus, people and technology work together to improve productivity.
Many experts agree that robots aren’t replacing human workers but instead filling low-skilled roles that people don’t want to fill. According to a Gartner survey, nearly 60% of supply chain professionals investing in automation say that labor constraints are their main motivation.
“Many businesses are struggling to find labor and to retain labor. We have to think about how we're treating [employees] so that we can retain and attract them. [Automation] is there to aid a human in doing work that used to be physically stressful, possibly mundane.” — Kim Baudry, market development director at Dematic
Benefits of warehouse automation
Some experts project that warehouse automation will grow by over 10% each year—and the reason why is clear. An automated warehouse has many benefits, including the following:
- More efficient inventory management
- Fewer stockouts or overstocks
- Reduced labor costs
- A safer working environment
- Optimized space utilization
- Faster order processing and fulfillment
- Fewer picking and packing errors
- Greater data visibility
- Ability to scale operations seamlessly
Later in this article, we’ll explore the benefits associated with specific automation solutions.
The two types of warehouse automation
The two types of warehouse automation—physical and digital automation—work together seamlessly to facilitate the smooth flow of goods. Let’s take a closer look at the differences between them.
Physical warehouse automation
Physical warehouse automation consists of machines and technology such as robotics. Because this kind of automation requires a significant upfront investment, it’s best suited for large warehouses with high shipping volumes. Physical automation improves the efficiency and reliability of warehouse processes, making it easier to scale.
Examples of physical automation include automated storage and retrieval systems and automated mobile robots. For more physical automation solutions, see the section below titled “Warehouse automation technology.”
Dematic’s AutoStore™ (pictured below) is an example of physical automation; the solution saves space and improves picking efficiency.
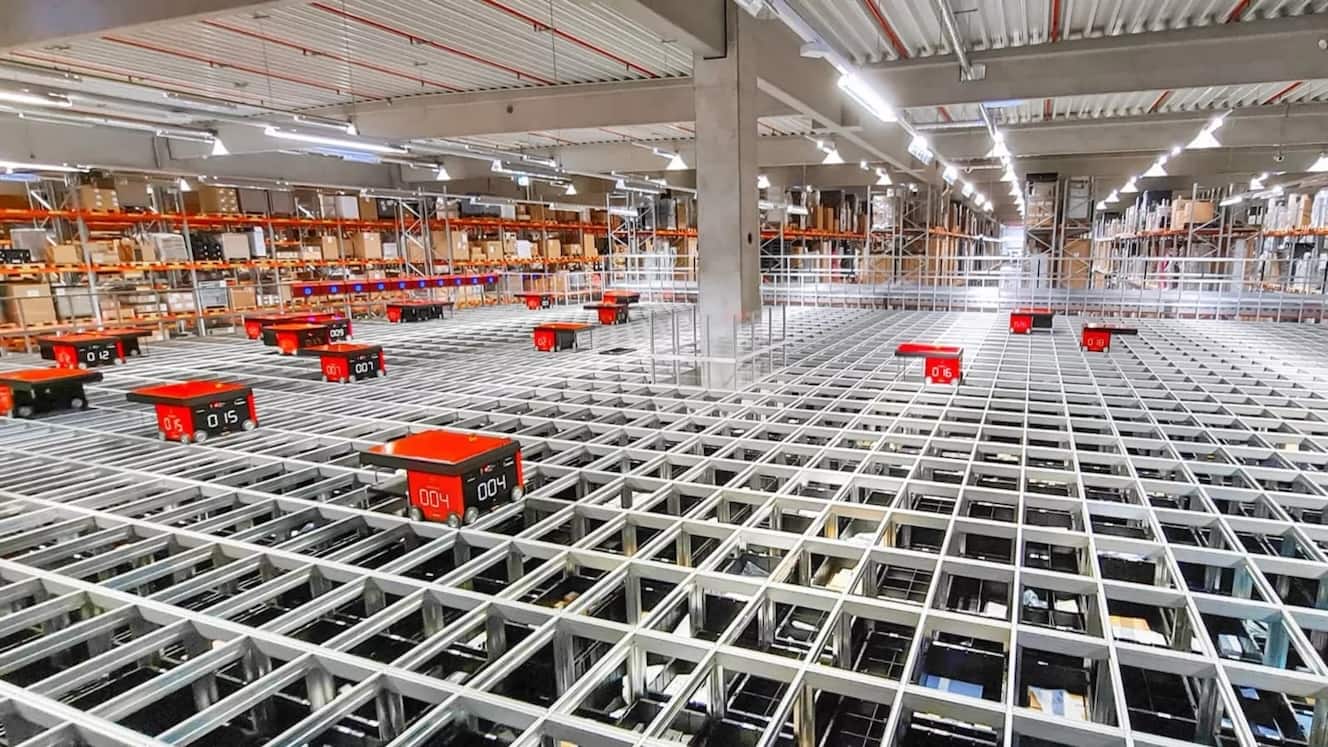
Digital warehouse automation
Digital warehouse automation consists of software. These systems facilitate the work of both robots and human employees by collecting and analyzing data and then providing suggestions to optimize workflows. For example, a warehouse management system tracks inventory locations throughout a warehouse and can provide instructions to pickers to maximize picking efficiency.
Warehouse automation technology
Every warehouse is different, and the automation technology you add will depend on your business’s size, products, and shipping volume. This section will cover some of the most common types of warehouse automation.
Warehouse automation software
Various software systems automate warehouse operations, leading to greater efficiency and lower costs.
Software | Processes it automates |
---|---|
Warehouse management system (WMS) | Inventory tracking, replenishment, order fulfillment, labor management |
Order management system (OMS) | Order processing, allocation, and routing; provides visibility into order status and inventory availability |
Inventory management system | Demand forecasting, inventory replenishment; provides visibility into stock levels and location |
Shipping software | Rate comparison, label generation, shipment tracking, documentation management |
Other systems commonly used to streamline warehouse processes include labor management systems, slotting optimization software, warehouse control systems, yard management systems, and supply chain visibility platforms.
Automated storage and retrieval systems (AS/RS)
Automated storage and retrieval systems (AS/RS) are robotic systems that automatically store and retrieve inventory from various locations within a warehouse or distribution center. They’re a type of goods-to-person (GTP) technology, or technology in which robots or machines bring items to people for picking and packing.
An AS/RS typically consists of storage racks, automated guided vehicles (AGVs) or robotic shuttles, conveyors, and computerized control systems.
When goods need to be stored, the AS/RS moves them from a loading area to an available storage location and places them using robotic arms or shuttles. When goods need to be retrieved, the AS/RS locates the requested items and delivers them to a designated picking area or shipping station.
AS/RS speeds up storage, retrieval, and replenishment, reducing the time and labor required for these tasks. It also maximizes warehouse space utilization by storing goods in dense configurations, such as high-rise storage racks.
Autonomous mobile robots (AMRs)
Autonomous mobile robots (AMRs) are robotic systems that use sensors, cameras, and navigation software to move autonomously within a warehouse or distribution center. They transport goods, pallets, or containers between different locations within the facility without the need for fixed infrastructure such as conveyors or tracks.
Because AMRs navigate dynamically, they can adapt to changes in the environment and avoid obstacles in real time. They’re generally a good investment for warehouses with large floor areas, complex layouts, or seasonal fluctuations in demand.
Automatic guided vehicles (AGVs)
Automatic guided vehicles (AGVs) are mobile robots that can navigate and transport materials within a warehouse without human intervention. Unlike AMRs, which navigate independently and respond to changes in their environments, AGVs follow predefined paths or routes using navigation technologies such as magnetic tape or laser guidance.
When goods need to be moved, AGVs receive instructions from a central control system and travel to the designated pickup location. Once the goods are loaded onto the AGV, it transports them to the desired destination.
Collaborative mobile robots
Collaborative mobile robots, also known as cobots, are designed to work alongside human workers in a shared workspace. These robots can perform a wide range of tasks—including loading and unloading, transportation, and picking—while collaborating with human workers to improve productivity and efficiency. By speeding up repetitive or physically demanding tasks, they allow humans to focus on more skilled or value-added activities.
Cobots can be programmed easily, which makes them highly versatile. And because they can be rented during high-demand seasons, they can help businesses avoid the need to lay off workers during slow times and rehire during busy periods.
Pick-to-light and put-to-light systems
Pick-to-light and put-to-light systems are used to improve order picking and sorting processes. They’re particularly useful in environments with many SKUs and frequent order turnover.
In a pick-to-light system, LEDs are installed at storage locations throughout the warehouse. When an order needs to be picked, the system uses the lights to show pickers where to find each item and how many to pick. The picker follows the instructions displayed on the lights, picking the required quantity from each location. Pick-to-light systems are very accurate, so they help reduce picking errors.
Put-to-light systems are used in sorting or packing areas. Similar to pick-to-light, LEDs are installed at sorting destinations or packing stations. When items need to be sorted or packed, the system uses lights to show the destination for each item. Workers place the items into the corresponding bins or containers, and once all items have been sorted or packed, the system confirms the completion of the task.
Voice picking and tasking
Voice picking and tasking solutions use voice recognition software and wearable devices to guide workers through their activities via spoken instructions.
In a voice picking system, workers wear lightweight, hands-free devices such as headsets or smart glasses equipped with microphones and speakers. When a worker receives a picking task, the system verbally instructs them on the item to pick, along with its location within the warehouse. Once the item is picked, the system updates the inventory records accordingly.
Voice tasking extends the use of voice technology beyond picking to other warehouse activities such as receiving, replenishment, packing, and cycle counting.
Automated sortation systems
Automated sortation systems sort and route goods to their designated destinations. They often include conveyor systems, mechanical sorting devices, barcode scanners, RFID readers, and vision systems.
Wearable technology
Wearable technology refers to devices worn by workers to enhance safety, productivity, and efficiency in their tasks. The following examples are commonly used in warehouse environments:
- Barcode scanners. Wearable barcode scanners are worn on the hand, wrist, or finger and allow workers to scan barcodes and QR codes without needing to hold a separate scanning device. This hands-free approach allows employees to scan items quickly and efficiently.
- Smart glasses. Smart glasses use augmented reality (AR) technology to give workers real-time information. They provide both audio and visual instructions to help employees navigate the warehouse, pick products, or troubleshoot issues.
- Exoskeletons. Exoskeletons are wearable devices that help employees perform physically demanding tasks like lifting, carrying, or repetitive motion. They reduce the risk of strain injuries and fatigue, helping workers perform tasks more safely and comfortably.
Industrial IoT
Internet of Things (IoT) refers to the integration of internet-connected devices and sensors to collect, analyze, and exchange data. Sensors and devices are installed throughout facilities to monitor factors such as equipment performance, environmental conditions, and energy consumption. These sensors collect data, which is then transmitted over networks to cloud-based platforms or edge-computing devices for processing and analysis.
IoT technology speeds up warehouse processes such as inventory management, predictive maintenance, and supply chain logistics by providing real-time insights into your operations.
Drones
Drones are aerial vehicles equipped with sensors, cameras, and GPS technology that can fly autonomously or be remotely controlled. In warehouses, drones can be used for things like inventory management, asset tracking, and facility monitoring.
When to automate your warehouse
Should you invest in automation for your facilities? When deciding whether the time is right to automate your warehouse, ask yourself these questions:
- Do your current technologies support automation? If current automation solutions, such as your WMS or shipping software, are outdated, solve those issues before attempting to add new technology. Collaborate with your IT department to ensure automation implementation will go smoothly.
- Is automation necessary to meet future demand? It’s no secret—warehouse automation can be a huge investment. If your warehouses are currently able to handle demand, with no signs of coming volume increases, automation may not be justified yet. On the other hand, if you predict a sharp increase in shipping volume, you should prepare now to meet that demand.
- Are you facing high labor costs and/or low worker availability? Having difficulty hiring employees is a sign that automation can help streamline and scale your operations. You can also look at whether you need to hire workers during high-demand seasons. Automation can help you scale up or down, reducing the need for a fluctuating workforce.
- Is your order fulfillment error-prone? If you’re experiencing low picking accuracy, order fill rates, or on-time deliveries, consider automating your picking, packing, and inventory management processes.
- Do your workers frequently get hurt or tired? If many workers are getting injured from lifting or reaching for objects, it may be time to make their jobs easier with technology.
Note: If you’d rather work with a 3PL than run your own distribution centers, you can still access the benefits of automation. Third-party logistics providers such as Nimble use robotics and software to facilitate fast, accurate deliveries.
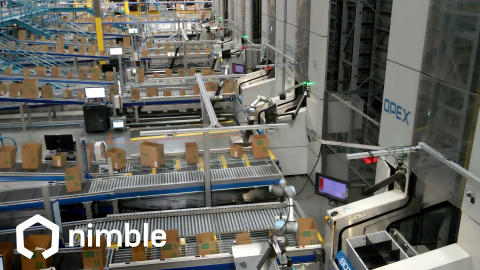
How to get started with warehouse automation
Ready to automate your warehouse? Follow the steps below to ensure your organization chooses the right solution and fully embraces the change.
Know your goals
Before diving into warehouse automation, define your objectives clearly.
First, determine what you aim to achieve with automation, whether it's reducing operating costs, improving service levels, increasing storage capacity, or another outcome. Understanding these goals ensures that the solutions you eventually implement will address specific pain points within your operations.
Next, decide whether your automation strategy will involve physical systems, digital solutions, or both. Consider engaging consultants to assess your needs and recommend solutions tailored to your warehouse environment.
Put together an implementation committee
Who will be the key decision-makers during automation planning and implementation? To keep things organized and avoid disrupting your current operations, assign people to spearhead the project.
Start by forming an implementation committee with representatives from finance, operations, IT, HR, and other relevant departments. This team will oversee the automation project, developing a plan that outlines the scope, schedule, and deliverables of the implementation process.
They’ll also establish a timeline and budget, assign project managers, get feedback from managers across departments, and track milestones and checkpoints to make sure the project is on track.
Review current procedures and determine KPIs
Once the implementation team has laid out guidelines and a timeline for the automation project, they should evaluate existing warehouse procedures, from inventory management to order fulfillment, to identify areas where automation can streamline operations and improve efficiency.
In addition, they should determine the key performance indicators (KPIs) that will measure the success of the automation efforts.
Create a plan
In order to effectively automate your facilities, you need to understand what technology you need, who provides it, and what the advantages and disadvantages are.
Research a variety of automation technologies and vendors to identify solutions that best fit your requirements. Explore sourcing and partnership options to leverage external expertise and resources if needed. Your plan should align with long-term business objectives, taking into account demand, time and resources, and feedback from managers.
Don’t forget about people!
Warehouse automation won’t just transform processes—it will also impact the roles and responsibilities of your workforce. When used correctly, automation can provide more opportunities for career development, which will improve your recruiting and retention.
Automate with your human workers in mind, redesigning roles when necessary. Invest in training and upskilling programs so that employees can operate and maintain advanced automation systems.
If you prioritize communication and change management, you’ll create a culture of adaptability and collaboration throughout your organization’s automation journey.
Automate your shipping with EasyPost
Picking and packing generally tend to be the stars of the distribution center show. But what about shipping? Every time a new customer order comes in, you need to create a shipping label with the right carrier, service level, and destination address. Some businesses use outdated or cobbled-together systems to create these shipping labels, but that can bog down processes, keeping them from meeting on-time delivery goals.
Automation can help! EasyPost’s suite of shipping APIs allows you to automate every element of the shipping process, from carrier selection to shipment tracking.
Speed up shipping and eliminate errors with EasyPost—it’s free to get started.